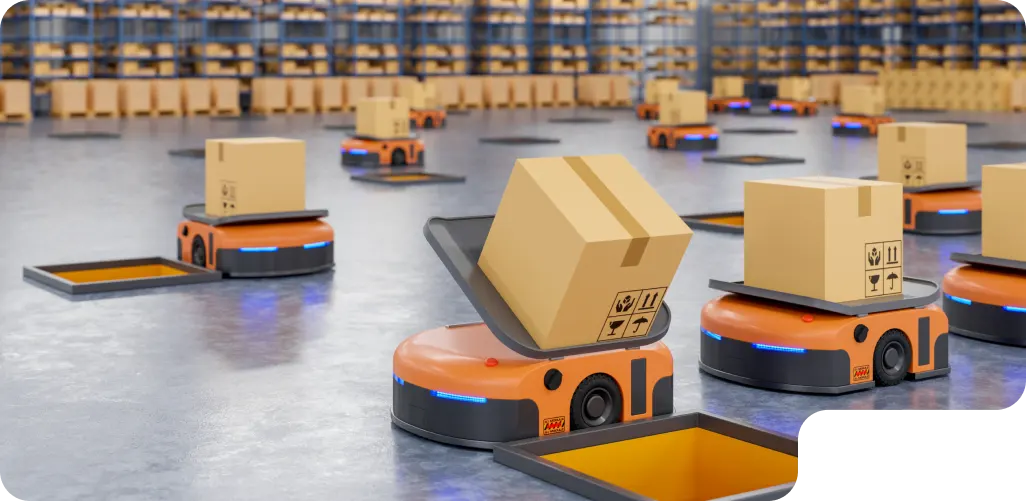
Welcome to a comprehensive exploration of “E-commerce Fulfillment Best Practices: From Warehouse to Doorstep.” In the dynamic world of online commerce, successful order fulfillment extends beyond mere product delivery—it’s a journey that demands strategic precision and customer-centric excellence. In this guide, we embark on a journey through the intricate process of transforming a customer’s virtual order into a tangible experience at their doorstep.
From optimizing warehouse operations to mastering packaging techniques and selecting the most suitable shipping methods, we delve deep into the realm of e-commerce fulfillment.
What is Order Fulfillment?
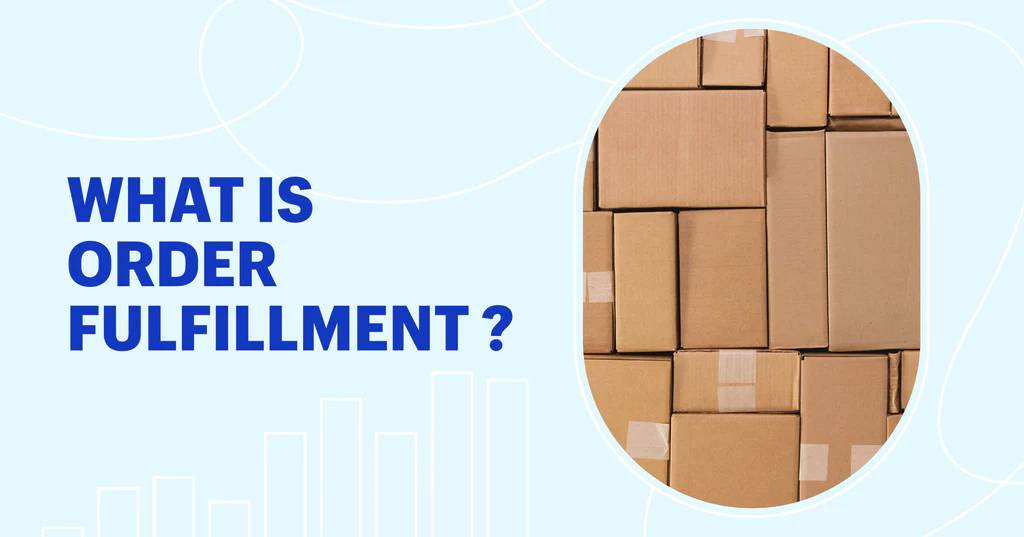
Order fulfillment refers to the entire process of receiving, processing, assembling, packaging, and delivering customer orders. In the context of e-commerce, order fulfillment encompasses all the steps involved in preparing and shipping products to customers who have made purchases through online platforms.
Efficient order fulfillment is essential for maintaining customer satisfaction and loyalty. A seamless fulfillment process ensures that customers receive their orders accurately and in a timely manner, contributing to a positive overall shopping experience. Businesses often invest in technology, such as order management systems and warehouse management systems, to streamline and automate these processes.
Order Fulfillment Process
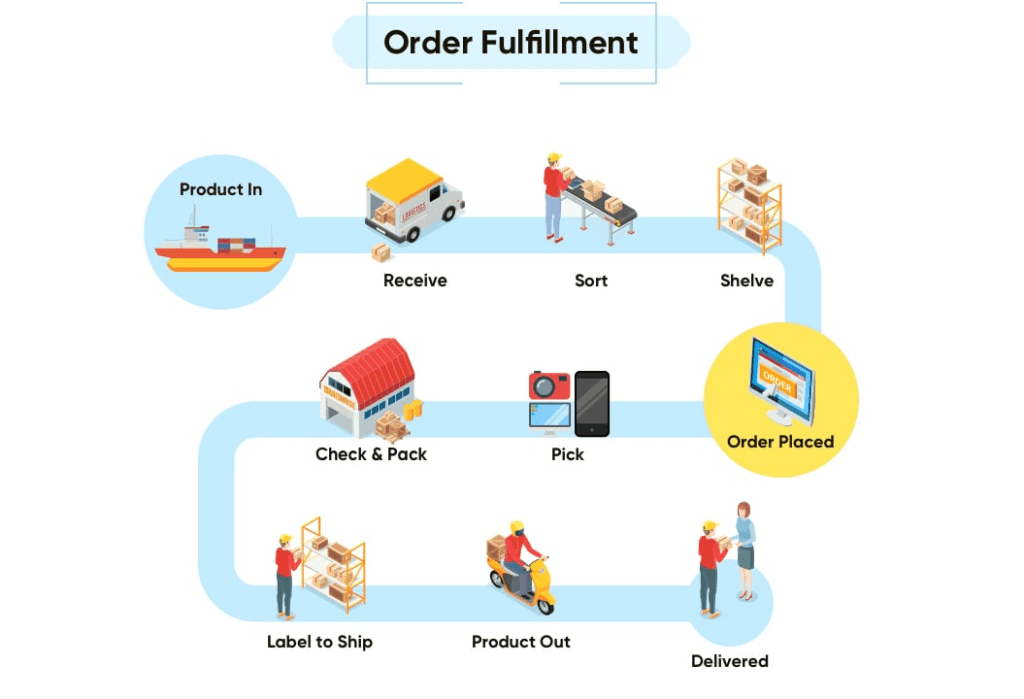
Receiving:
- Incoming shipments of products are received at the warehouse.
- The received items are inspected for damage and accuracy against the provided packing list.
- The inventory management system is updated to reflect the new stock.
Inventory Storage:
- Organized and store products in designated locations within the warehouse.
- Categorize items based on factors like size, type, and demand.
- Efficient warehouse layout ensures easy access and minimizes storage space.
Order Processing:
- Customer orders are received through various sales channels (e.g., website, marketplace).
- The order management system processes and verifies the order details.
- Inventory levels are checked to ensure items are in stock.
Picking and Packing:
- The order is prepared for fulfillment by selecting the required items from their storage locations.
- Efficient picking methods (e.g., batch picking, zone picking) optimize the process.
- Picked items are then brought to the packing area.
Shipping:
- Shipping labels and tracking information are generated for each order.
- The order is handed over to the selected shipping carrier for delivery.
- The carrier transports the package to the specified destination.
Returns Processing:
- If a customer wishes to return a product, the returns process is initiated.
- The returned item is inspected to determine its condition and eligibility for resale.
- Depending on the condition, the item may be restocked, refurbished, or discarded.
Efficient coordination and integration of technology systems are essential for a smooth and seamless fulfillment process.
Planning Your Order Fulfilment Strategy
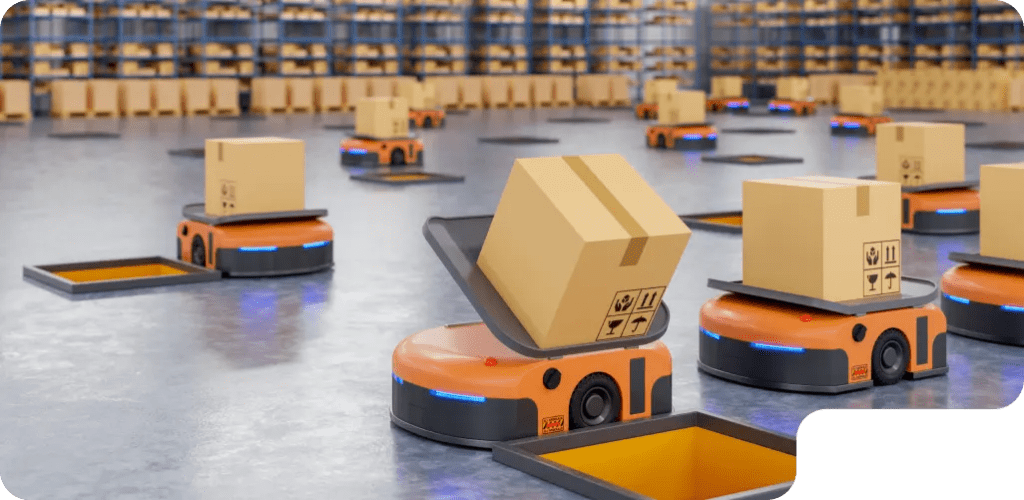
Planning your order fulfillment strategy is crucial for ensuring a seamless and efficient process that meets customer expectations and supports business growth. Here’s a guide to help you plan your order fulfillment strategy effectively:
Understand Customer Expectations:
- Determine customer preferences for shipping speed, packaging, and tracking.
- Consider offering multiple shipping options to cater to various customer needs.
Assess Your Product Range:
- Categorize products based on their size, fragility, and demand.
- Different products may require distinct fulfillment approaches.
Choose Fulfillment Models:
- Decide between in-house fulfillment, third-party logistics (3PL), dropshipping, or a combination.
- Consider factors like control, cost, and scalability when making this choice.
Optimize Inventory Management:
- Implement inventory management software to track stock levels in real-time.
- Set reorder points, safety stock levels, and adopt an efficient replenishment strategy.
Lay Out Warehouse Layout:
- Organize your warehouse for efficient product storage and retrieval.
- Prioritize high-demand items for easy access and plan for growth.
Streamline Order Processing:
- Implement an order management system to automate order processing and reduce errors.
- Integrate your e-commerce platform with your fulfillment process for seamless data flow.
Choose Packaging Materials:
- Select packaging materials that protect products during transit while also representing your brand.
- Consider eco-friendly options to align with sustainability goals.
Optimize Pick and Pack Process:
- Use efficient picking methods like batch picking or zone picking to minimize travel time.
- Train staff on proper packing techniques to ensure consistent quality.
Shipping and Carrier Selection:
- Partner with reliable shipping carriers and negotiate favorable rates.
- Offer customers various shipping options based on their preferences and budget.
Implement Returns Management:
- Develop a clear returns policy that is easy for customers to understand.
- Plan for efficient returns processing, including inspection, restocking, or refurbishing.
Monitor and Analyze Performance:
- Track key performance indicators (KPIs) such as order accuracy, fulfillment speed, and shipping costs.
- Regularly analyze data to identify areas for improvement and growth.
Prepare for Peak Seasons:
- Anticipate increased order volumes during holidays and promotions.
- Scale up staffing, inventory, and resources to meet peak demand.
Continuously Improve:
- Regularly assess and refine your fulfillment strategy based on customer feedback and evolving market trends.
- Stay adaptable to changes in technology, customer behavior, and industry best practices.
Planning your order fulfillment strategy requires careful consideration of customer needs, efficient processes, and scalability. By focusing on these aspects, you can build a fulfillment strategy that enhances customer satisfaction and supports the growth of your e-commerce business.
E-commerce Fulfillment Best Practices
Accurate Inventory Management
Maintain real-time visibility of your inventory across all sales channels. Implement a robust inventory management system to prevent stockouts and overstocking.
Efficient Order Processing
Process orders promptly and accurately. Automate order processing wherever possible to reduce manual errors and save time.
Optimized Warehouse Layout
Organize your warehouse for efficient product storage and easy navigation. Group products logically and prioritize high-demand items for quick access.
Effective Pick and Pack Processes
Implement efficient picking methods like batch picking or zone picking to minimize time spent searching for products. Train staff to pack orders securely and consistently.
Quality Control Checks
Conduct quality checks to ensure that they pick and pack the correct items, and that they meet quality standards before shipping.
Packaging Excellence
Choose appropriate packaging materials to protect products during transit. Consider sustainable packaging options to align with eco-conscious consumer preferences.
Multiple Shipping Options
Offer various shipping methods to cater to different customer preferences. Provide estimated delivery times and tracking information for transparency.
Clear Returns Policy
Develop a customer-friendly returns policy that is easy to understand. Make the returns process simple and hassle-free to build trust with customers.
Customer Communication
Keep customers informed throughout the fulfillment process. Send order confirmation emails, shipping notifications, and delivery updates.
Technology Integration
Integrate your e-commerce platform, order management system, and inventory management software to streamline data flow and automate processes.
Continuous Improvement
Regularly analyze performance metrics and gather customer feedback to identify areas for improvement. Adapt your strategies based on insights gained.
Scalability Planning
Design your fulfillment process to accommodate growth. Consider factors like warehouse space, staffing, and technology upgrades.
Sustainable Practices
Incorporate eco-friendly practices where possible, such as optimizing shipping routes to reduce carbon emissions and minimizing excess packaging.
Employee Training and Engagement
Train your staff thoroughly in fulfillment procedures, quality control, and customer service. Engaged and knowledgeable employees contribute to a smoother process.
These best practices can help you establish a strong foundation for efficient and customer-focused e-commerce fulfillment operations. Tailor them to your business’s specific needs and continually refine your processes to adapt to changing market dynamics.