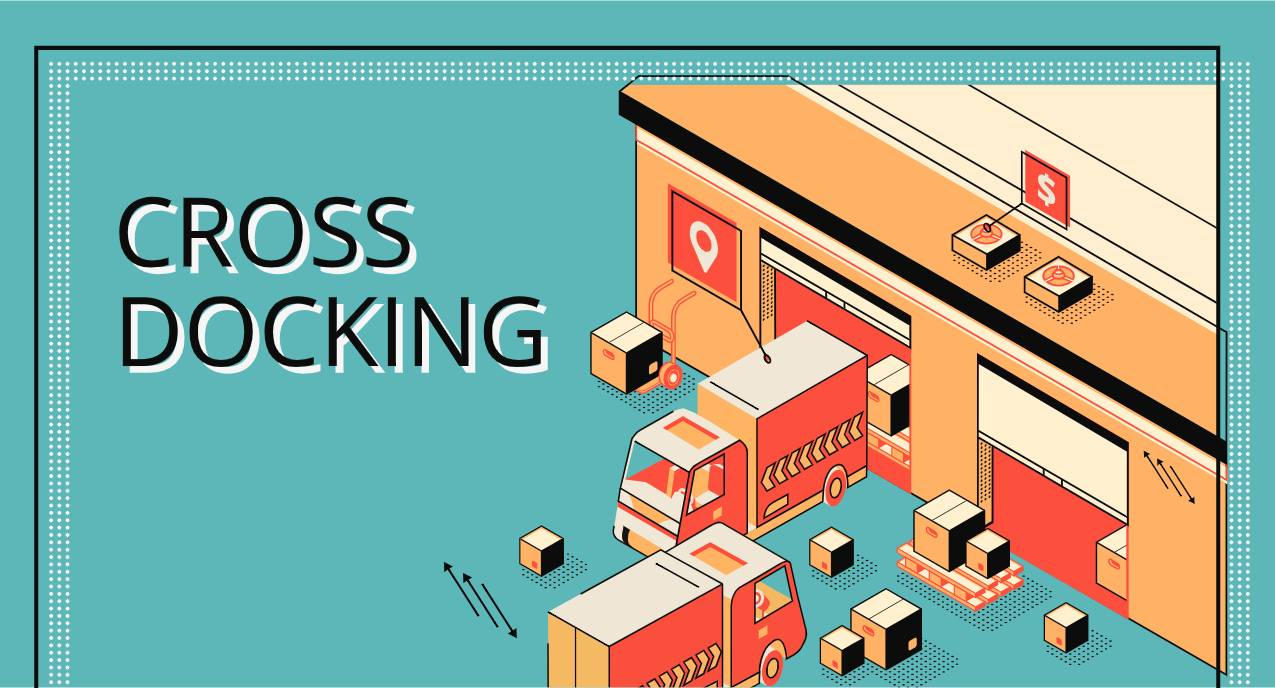
Cross-docking is a logistics strategy that has gained significant attention in recent years due to its potential to streamline supply chain operations and enhance efficiency. In today’s fast-paced world of commerce, businesses are constantly seeking innovative ways to reduce costs, minimize inventory holding, and deliver products to consumers more rapidly. emerges as a solution that addresses these challenges head-on.
In this comprehensive guide, we will delve into the intricacies of this logistics technique.
What is cross-docking?
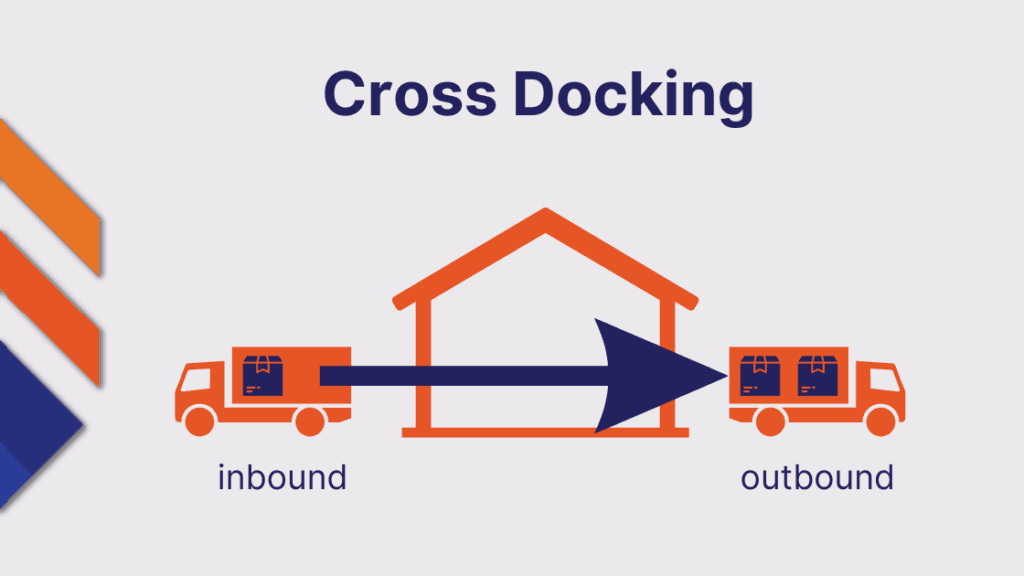
Cross-docking is a logistics and supply chain management strategy designed to efficiently transfer goods from incoming shipments to outgoing ones with minimal or no storage time in between. It is a distribution process where products are unloaded from an inbound vehicle, such as a truck or container, and then immediately loaded onto an outbound vehicle, like another truck or trailer, often without the need for warehousing or long-term storage.
Types of cross-docking
can be categorized into various types, each tailored to specific supply chain and distribution needs. These types of cross-docking are as follows:
Retail Cross-Docking
Retail cross-docking is commonly used in the retail industry. It involves receiving products from multiple suppliers and then immediately sorting and shipping them to individual retail stores. This method ensures that each store receives the specific merchandise it requires without the need for intermediate storage. Retailers can respond rapidly to changes in consumer demand and seasonal trends by using retail cross-docking.
Manufacturing Cross-Docking
Manufacturing cross-docking focuses on the efficient delivery of components, materials, or parts directly to the production line. Suppliers deliver these items precisely when they are needed in the manufacturing process. This approach supports just-in-time (JIT) manufacturing, minimizes inventory holding costs, and enhances production efficiency. Manufacturers can reduce storage space requirements and optimize production schedules through manufacturing cross-docking.
Distributor Cross-Docking
Distributor cross-docking involves consolidating shipments from various suppliers at a distribution center and then redistributing them to retailers, wholesalers, or customers. This method optimizes transportation and reduces handling by consolidating shipments into larger, more efficient loads. Distributors play a critical role in coordinating and synchronizing the flow of goods to meet customer demand effectively.
Opportunistic Cross-Docking
Opportunistic cross-docking is a dynamic approach that involves seizing opportunities as they arise. It includes combining partial shipments into full loads, making last-minute adjustments to distribution plans, or rerouting products in response to unforeseen events such as supply disruptions or unexpected customer demand spikes. This type of requires agility and adaptability in supply chain operations.
Cross-Docking with Value-Added Services
Some cross-docking operations may include value-added services, such as packaging, labeling, quality control inspections, or product assembly. These additional services can be integrated into the cross-docking process to meet specific customer requirements or to enhance product quality before shipment.
Deferred Cross-Docking
Deferred cross-docking involves temporarily storing incoming goods before they are sorted and shipped to their final destinations. While it may involve some storage, the goal is still to minimize storage time as much as possible. This approach is often used when there are slight delays in matching supply with demand or when additional quality checks are necessary.
The choice of cross-docking type depends on the specific industry, supply chain structure, product characteristics, and business objectives. Companies can adopt a combination of these cross-docking types or tailor their approach to best meet their operational needs and customer demands. Successful cross-docking implementation requires effective planning, coordination, and technology integration to optimize supply chain efficiency.
Benefits of cross-docking
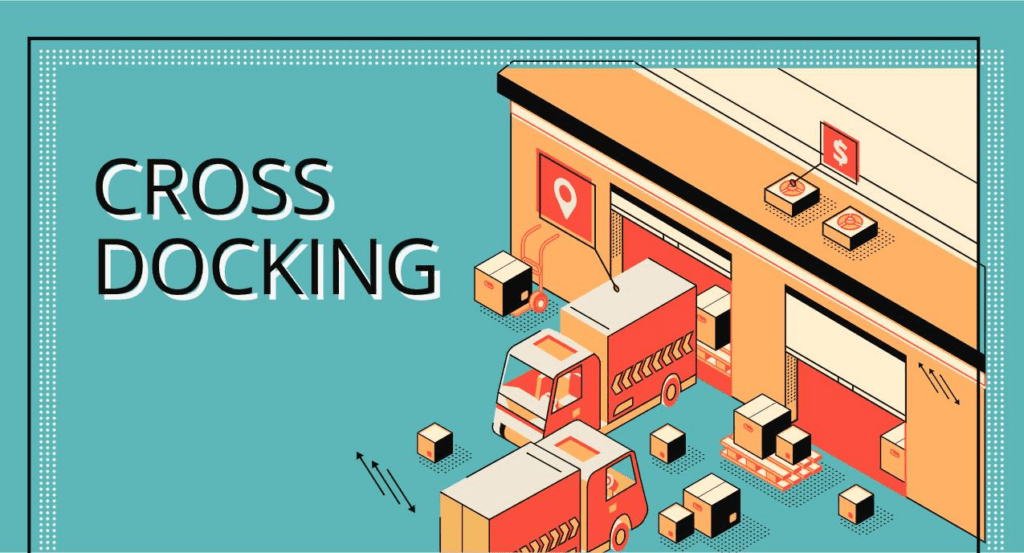
It offers several significant benefits to businesses that incorporate this logistics strategy into their supply chain operations. Here are some key advantages:
Reduced Inventory Costs
One of the most notable benefits of this logistics technique is the reduction in inventory holding costs. Since they move products quickly through the facility without the need for long-term storage, businesses can minimize expenses related to warehousing, storage space, and associated carrying costs. This lean inventory approach can lead to substantial cost savings.
Faster Product Turnaround
It enables rapid product turnover. Incoming goods are immediately sorted and loaded onto outgoing vehicles, which means shorter processing times. This speed is especially advantageous for industries where timely delivery is crucial, such as retail, perishable goods, or industries with just-in-time (JIT) manufacturing processes.
Lower Transportation Costs
By consolidating shipments and optimizing transportation routes, it can reduce transportation costs. Businesses can achieve more efficient truckload utilization, eliminate unnecessary stops or transfers, and minimize fuel expenses. This results in cost savings while also reducing the environmental footprint of transportation operations.
Enhanced Supply Chain Flexibility
It enhances supply chain flexibility and responsiveness. It allows for quick adjustments to shifts in customer demand, supply disruptions, or changes in distribution patterns. Businesses can adapt more swiftly to market dynamics and ensure products reach their destinations on time.
Improved Product Quality and Handling
It can lead to improved product quality and reduced handling-related damages. Since products spend less time in storage and are moved directly from inbound to outbound vehicles, there is less risk of damage, spoilage, or deterioration due to extended storage periods.
In addition to these five benefits, can also contribute to better use of labor resources, reduced order cycle times, and increased overall supply chain efficiency. However, it’s important to note that implementing cross-docking successfully requires careful planning, coordination, and integration with other supply chain processes to realize these advantages fully.