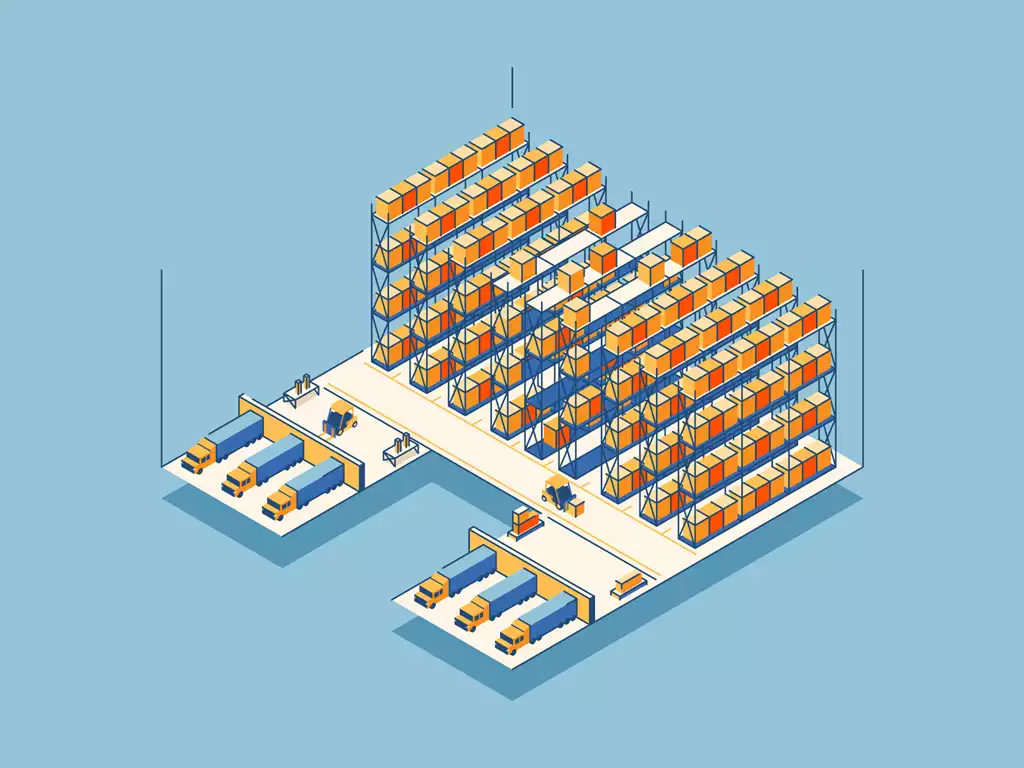
Setting up an efficient warehouse is a pivotal undertaking for businesses seeking to streamline operations, enhance productivity, and meet the demands of a dynamic market. The effective organization and management of a warehouse not only impact inventory control but also influence overall supply chain efficiency. In today’s competitive business landscape, where speed and accuracy are paramount, a well-structured warehouse becomes a strategic asset.
This guide explores the key principles and considerations involved in establishing an efficient warehouse, addressing factors ranging from layout planning and technology integration to workforce optimization.
What is a warehouse layout?
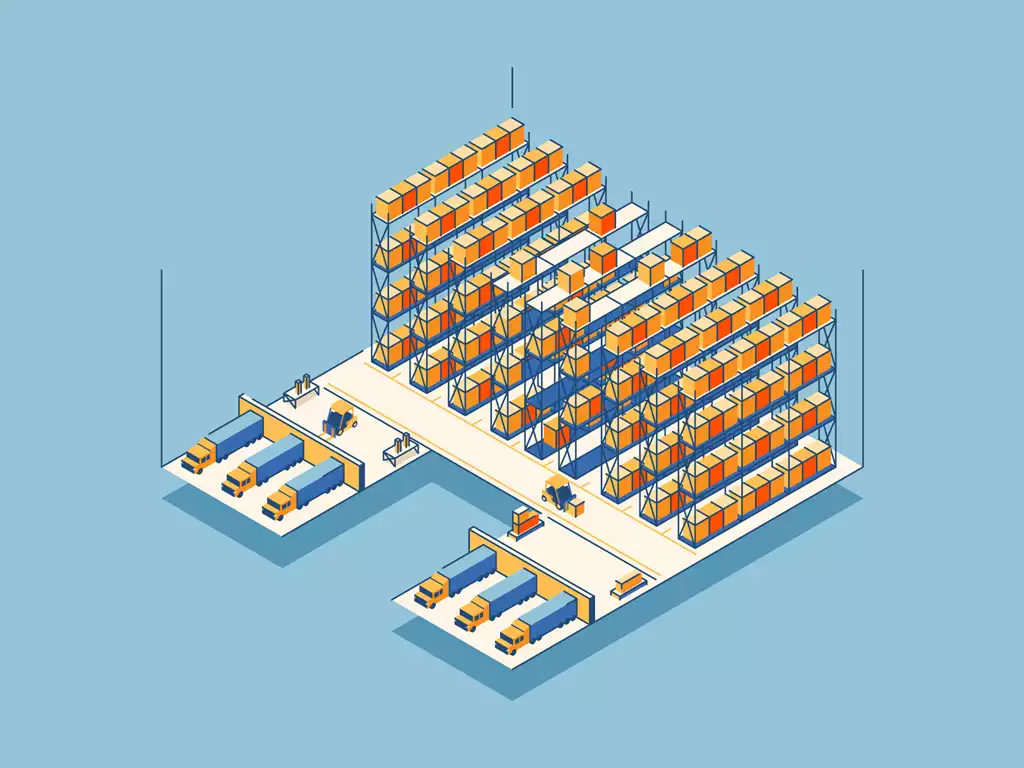
It refers to the physical arrangement and organization of the different areas within a warehouse facility. It involves strategically positioning storage areas, workspaces, aisles, and other functional zones to optimize the flow of goods, streamline operations, and maximize the use of available space. The warehouse layout is a critical aspect of logistics and supply chain management, influencing the efficiency and productivity of the entire warehouse operation.
What factors affect the layout plan?
The layout plan of a warehouse is crucial for optimizing efficiency, productivity, and overall operational effectiveness. Several factors influence the design and arrangement of a warehouse. Here are some factors:
Inventory Characteristics
The type, size, and nature of the inventory play a significant role in determining the layout of a warehouse. Items with different storage requirements (e.g., temperature-sensitive goods, hazardous materials, perishable items) may necessitate specific storage zones or areas with appropriate conditions.
Material Handling Equipment
The choice and availability of material handling equipment (MHE) impact . Different types of equipment, such as forklifts, conveyor systems, and automated guided vehicles (AGVs), may require specific aisle widths, turning radii, and clearances, influencing the overall spatial configuration of the warehouse.
Order Picking Methodology
The method used for order picking (e.g., batch picking, zone picking, wave picking) influences the layout. Efficient order fulfillment often requires strategically placing products and organizing picking paths to minimize travel time for workers and increase overall picking speed.
Flow of Goods and Information
A smooth flow of goods and information is essential for a well-functioning warehouse. The layout should facilitate a logical progression of goods from receiving through storage to shipping. Additionally, the flow of information, including communication systems and technology infrastructure, should be integrated into the layout to optimize overall operational efficiency.
Space Utilization and Expansion Plans
It should maximize the use of available space while allowing for future expansion. Factors such as storage density, aisle widths, and vertical storage options impact space utilization. Flexibility and scalability are critical considerations to accommodate changes in inventory volume or shifts in business requirements.
These factors are interconnected, and a well-designed warehouse layout takes into account the specific needs and priorities of the business to create an efficient and adaptable operational environment.
How do you set up an efficient warehouse?
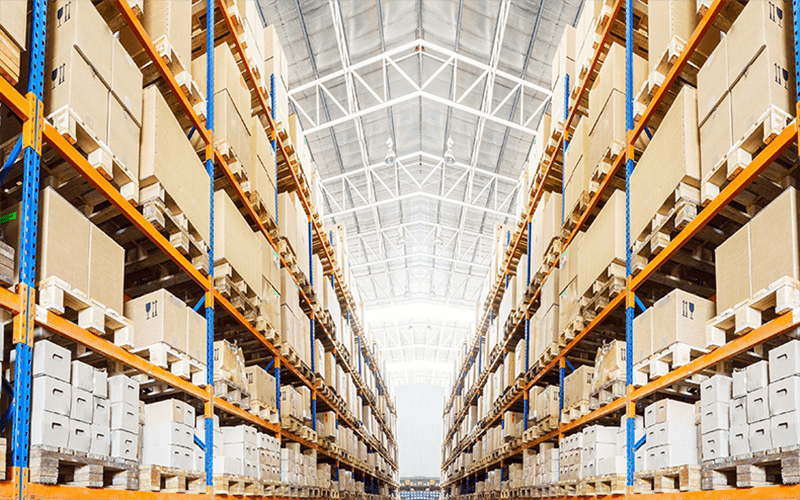
Setting up an efficient warehouse involves careful planning and consideration of various factors to streamline operations, improve productivity, and enhance overall logistics management. Here are steps to set up:
Optimize Warehouse Layout and Design:
- Zoning: Divide the warehouse into functional zones, such as receiving, storage, picking, packing, and shipping. Ensure a logical flow of goods through these zones to minimize unnecessary movement.
- Storage Systems: Choose appropriate storage systems based on the nature of your products. Options include pallet racking, shelving, mezzanine storage, or automated storage and retrieval systems (AS/RS).
- Clear Aisles: Designate clear and wide aisles to facilitate the movement of materials, equipment, and personnel. Ensure that pathways are free of obstacles to prevent congestion and accidents.
Implement Effective Inventory Management:
- Inventory Control Systems: Adopt a robust inventory management system, utilizing technologies like barcoding, RFID, or warehouse management system (WMS) software for real-time tracking and accuracy.
- ABC Analysis: Classify inventory based on its importance and allocate storage space accordingly. High-demand items should be easily accessible, while lower-demand items can be stored in less accessible areas.
Leverage Technology and Automation:
- Warehouse Management System (WMS): Implement a WMS to automate and optimize various warehouse processes, including inventory tracking, order picking, and replenishment.
- Automation Solutions: Explore automation technologies such as conveyor systems, robotics, or autonomous mobile robots (AMRs) to improve efficiency in material handling, order fulfillment, and inventory management.
Optimize Picking and Packing Processes:
- Batch Picking: Group similar orders together to minimize travel time and optimize picking routes. Batch picking can improve efficiency by reducing the number of trips pickers need to make.
- Use Efficient Packing Stations: Design packing stations with all necessary materials, equipment, and packaging supplies to expedite the packing process. Consider implementing automation for packaging tasks when feasible.
Focus on Employee Training and Safety:
- Training Programs: Provide comprehensive training programs for warehouse staff to ensure they are proficient in using equipment, following safety protocols, and understanding warehouse processes.
- Safety Measures: Prioritize safety by implementing proper signage, providing personal protective equipment (PPE), and conducting regular safety training. A safe work environment reduces the risk of accidents and injuries.
Continuous Improvement and Flexibility:
- Regular Audits: Conduct regular audits and performance assessments to identify areas for improvement. Analyze data and feedback to make informed decisions on optimizing processes.
- Adaptability: Design the warehouse layout and processes with adaptability in mind. Businesses should be able to adjust to changes in product demand, seasonal variations, or modifications in the supply chain.
Efficient warehouse setup is an ongoing process that requires continuous monitoring, analysis, and adaptation to meet evolving business needs and industry trends.