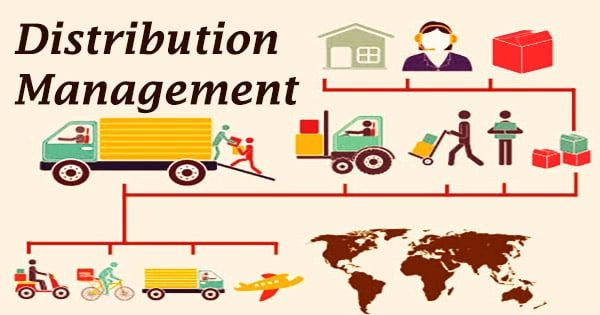
In the ever-evolving landscape of modern business, efficient distribution management stands as a cornerstone of success for companies across various industries. The art of orchestrating the seamless flow of goods from manufacturers to end-users lies at the heart of distribution management. This comprehensive guide delves into the essence of , unraveling its definition, exploring the advantages it offers, and addressing the inherent challenges it presents.
What is distribution management?
Distribution management, also known as distribution channel management, refers to the process of overseeing and coordinating the efficient movement of products or goods from the manufacturer or supplier to the end-users or customers. It involves the planning, execution, and control of various activities within the supply chain to ensure that products are delivered to the right place, at the right time, and in the right condition.
The primary goal of distribution management is to optimize the distribution process, reducing costs, minimizing lead times, and maximizing customer satisfaction. It involves managing multiple aspects of the distribution network, including inventory management, warehousing, transportation, order fulfillment, and logistics.
Benefits of distribution management systems
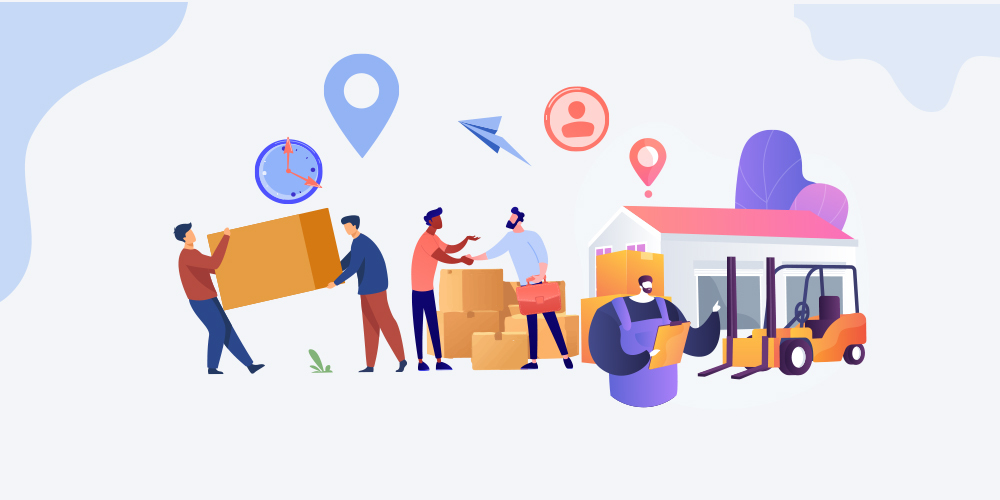
Distribution management systems offer a wide range of benefits to businesses involved in managing the supply chain and distribution processes. Here are six key benefits of using
Improved Inventory Management
Distribution management systems help optimize inventory levels by providing real-time visibility into stock levels, demand forecasts, and sales data. This ensures that companies can maintain optimal inventory levels, avoid stockouts, and reduce carrying costs.
Enhanced Order Fulfillment
Distribution management systems streamline order processing and fulfillment, enabling faster and more accurate order processing. This leads to improved on-time delivery rates and better customer satisfaction.
Efficient Logistics and Routing
These systems utilize advanced algorithms to optimize logistics and route planning, helping companies choose the most efficient transportation methods and routes. This results in reduced transportation costs, improved delivery times, and lower carbon footprints.
Centralized Data and Reporting
Distribution management systems centralize data from various points in the supply chain, providing businesses with a comprehensive view of their distribution operations. This data-driven approach allows for better decision-making, performance tracking, and identification of areas for improvement.
Real-time Tracking and Visibility
With distribution management systems, businesses can track the movement of goods in real-time, from the point of origin to the final destination. This visibility enables better control over shipments and allows for timely intervention in case of any issues or delays.
Streamlined Compliance and Documentation
Distribution management systems often integrate with customs and regulatory authorities, automating compliance processes and reducing paperwork. This simplifies cross-border operations, ensures adherence to legal requirements, and minimizes the risk of customs-related delays.
In summary, distribution management systems provide businesses with the tools and capabilities to optimize their supply chain and distribution processes. From improved inventory management to streamlined logistics and enhanced customer satisfaction, these systems offer a host of benefits that contribute to overall operational efficiency and competitiveness in today’s dynamic business landscape.
What are the 6 factors of distribution management?
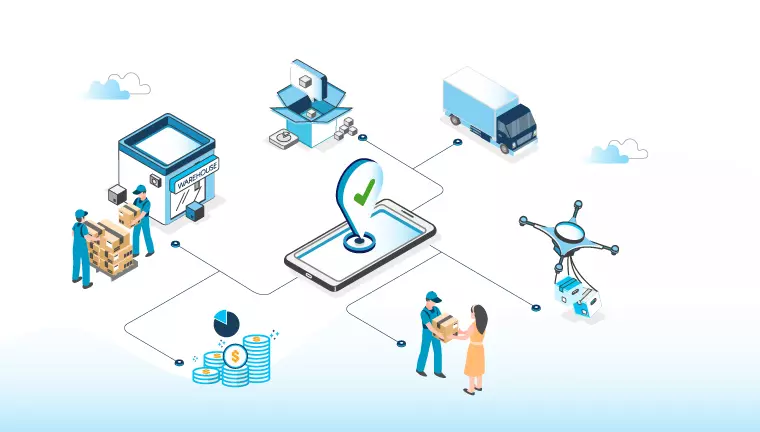
involves overseeing various aspects of the supply chain and distribution process.
Here are six key factors that are integral to effective distribution management:
Inventory Management
Efficient inventory management is essential in distribution management. It involves determining the right quantity of products to keep in stock to meet customer demands while minimizing carrying costs. Distribution managers must ensure optimal inventory levels, track stock movements, and plan for timely replenishment to avoid stockouts and overstocking.
Warehousing and Storage
Proper warehousing and storage facilities are crucial for distribution management. Distribution managers need to strategically plan the location and layout of warehouses to ensure smooth product flow and timely deliveries. Efficient storage and handling practices help maintain the integrity of goods and prevent damage.
Transportation and Logistics
It encompasses the planning, coordination, and optimization of transportation and logistics activities. This includes selecting the appropriate transportation modes (e.g., trucks, ships, planes), route planning, freight negotiation, and monitoring delivery schedules to ensure timely and cost-effective product distribution.
Order Fulfillment
The order fulfillment process is a critical factor in distribution management. Distribution managers need to streamline order processing, from order receipt to order picking, packing, and shipping. Efficient order fulfillment ensures that customer orders are processed accurately and delivered on time.
Distribution Network Design
The design of the distribution network is a fundamental factor in distribution management. Distribution managers must determine the optimal structure of the distribution network, including the number and location of distribution centers, warehouses, and retail outlets. A well-designed network helps minimize transportation costs and lead times while maximizing market coverage.
Technology and Data Management
Utilizing technology and data management tools is crucial in modern distribution management. Distribution managers need to leverage distribution management systems and other software to centralize data, track inventory, monitor logistics, and gain real-time visibility into the supply chain. Data-driven insights facilitate informed decision-making and continuous process improvement.
By effectively managing these six factors, distribution managers can optimize supply chain operations, improve customer satisfaction, reduce costs, and enhance overall distribution efficiency. A well-coordinated distribution management approach is vital for businesses seeking to gain a competitive edge in today’s global market environment.
What are the challenges of distribution management?
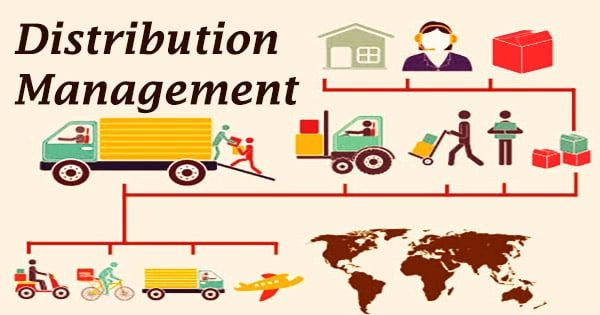
Distribution involves a complex set of activities and processes, and it comes with its own set of challenges.
Here are five common challenges faced in distribution management:
Inventory Management Complexity
Balancing inventory levels to meet customer demands while minimizing holding costs is a significant challenge. Overstocking ties up capital and leads to increased carrying costs, while understocking can result in stockouts and dissatisfied customers. Accurate demand forecasting and efficient inventory management systems are crucial to address this challenge.
Transportation and Logistics Costs
Transportation is a major cost factor in distribution. Finding cost-effective and reliable transportation solutions can be challenging, especially when dealing with various transportation modes, multiple delivery points, and diverse geographical locations. Rising fuel prices, capacity constraints, and traffic congestion add to the complexity of logistics management.
Order Fulfillment and Timely Delivery
Timely order fulfillment is essential for meeting customer expectations. Delays in order processing, picking, packing, and shipping can lead to customer dissatisfaction and impact brand reputation. Managing order complexities, ensuring accurate order processing, and minimizing delivery lead times are constant challenges for distribution operations.
Supply Chain Visibility and Communication
A lack of real-time supply chain visibility and communication can hinder efficient distribution. Issues in communication between suppliers, manufacturers, distributors, and retailers can lead to information gaps and disruptions in the distribution process. Collaborative technologies and effective communication channels are necessary to address this challenge.
Global Distribution Challenges
Companies engaged in global distribution face additional challenges such as navigating complex customs and trade regulations, dealing with diverse cultures, time zones, and language barriers. Ensuring compliance with international laws and managing cross-border logistics add layers of complexity to global distribution operations.
E-commerce and Omnichannel Distribution
The rise of e-commerce and omnichannel retailing presents new challenges for distribution. Companies need to manage multiple sales channels seamlessly, ensure consistency in inventory data across platforms, and provide fast and efficient fulfillment options to meet the demands of online shoppers.
Addressing these challenges requires strategic planning, investment in technology and automation, effective collaboration with supply chain partners, and a customer-centric approach. Distribution managers need to be proactive in identifying and resolving issues to optimize distribution efficiency and deliver a positive customer experience.