Buffer inventory, a strategic component of supply chain management, plays a pivotal role in shaping the operational efficiency and financial health of businesses across diverse industries. In the dynamic landscape of modern commerce, where uncertainties and fluctuations are inevitable, the concept of buffer inventory has gained paramount importance. This inventory acts as a safety net, safeguarding businesses against unforeseen disruptions in production, demand variability, and supply chain bottlenecks.
This exploration delves into the multifaceted impact that buffer inventory wields and sheds light on the ways it empowers businesses to navigate complexities and enhance their competitive edge.
What is buffer inventory?
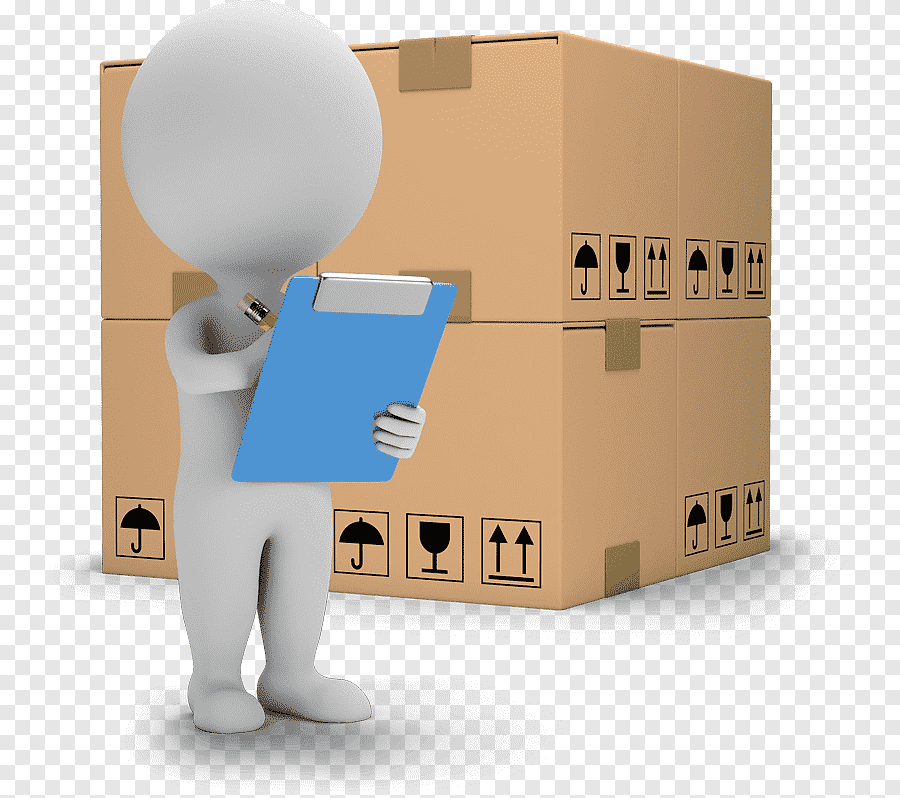
Buffer inventory, often referred to as safety stock, is a quantity of goods or materials that a company holds in reserve within its supply chain to mitigate the impact of uncertainties and variability in demand, supply, and production processes. This additional stock is strategically maintained above and beyond the anticipated requirements, acting as a cushion to absorb unexpected fluctuations in these factors.
It also serves as a mechanism to bridge the gap between demand and supply variability. In an environment where demand patterns are uncertain and suppliers may face challenges in maintaining consistent production rates, it provides a safety net to balance these fluctuations and maintain a certain level of service level or customer satisfaction.
Buffer inventory vs. safety stock
Buffer inventory and safety stock are terms often used interchangeably, as they refer to the same concept within supply chain management. Both buffer inventory and safety stock are additional quantities of goods or materials that a company holds beyond its anticipated demand in order to mitigate uncertainties and disruptions in the supply chain.
However, there can be slight differences in how these terms are used based on context and industry practices:
Buffer Inventory
This term is more general and encompasses any extra stock held in reserve to provide a buffer against uncertainties. It includes safety stock, but it can also refer to other types of extra inventory such as anticipation inventory (stock built up before a known event like a promotional sale) or hedge inventory (stock held in anticipation of price fluctuations).
Safety Stock
This term specifically refers to the inventory maintained to mitigate the risk of stockouts caused by fluctuations in demand or supply. Safety stock is often calculated using statistical methods that take into account factors such as demand variability, lead time variability, and desired service level. It’s intended to ensure that the company can meet customer demand even when unforeseen disruptions occur.
In essence, while both terms involve holding extra inventory for risk management purposes, “safety stock” is a more precise term that specifically addresses the goal of maintaining inventory to prevent stockouts due to uncertainties, while “buffer inventory” can encompass various types of additional stock held for risk mitigation.
In practical usage, you’ll often find these terms used interchangeably because the underlying concept of holding extra inventory for risk mitigation remains the same. The choice of terminology might depend on the industry, organizational preferences, or the specific context of the discussion
What are the advantages and disadvantages of buffer inventory?
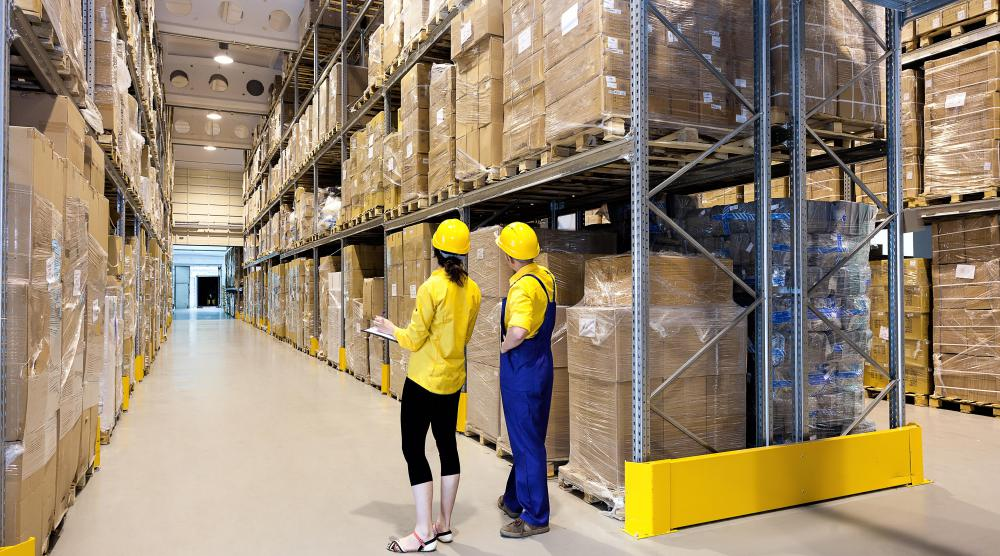
Buffer inventory, also known as safety stock, offers several advantages and disadvantages to businesses. Understanding these pros and cons is crucial for effectively managing inventory and supply chain operations:
Advantages
- Risk Mitigation: It acts as a cushion against supply chain disruptions, demand variability, and other uncertainties, reducing the risk of stockouts and associated negative consequences.
- Customer Satisfaction: Maintaining buffer inventory ensures that products are available even during unexpected spikes in demand, leading to higher customer satisfaction and retention rates.
- Operational Continuity: It helps prevent production stoppages caused by delays in material deliveries, ensuring uninterrupted production and efficient operations.
- Reduced Lead Time Impact: It compensates for variations in lead times due to supplier delays, transportation issues, or other factors, enabling businesses to meet customer demands on time.
- Optimized Production Scheduling: It can facilitate smoother production scheduling by absorbing minor disruptions and preventing bottlenecks.
- Supplier Relationship Improvement: Consistent order patterns due to buffer inventory can improve relationships with suppliers, as they can rely on stable demand, leading to potential collaboration and preferential treatment.
Disadvantages
- Higher Holding Costs: Holding excess inventory ties up capital and incurs costs related to storage, insurance, obsolescence, and potential interest on borrowed funds.
- Capital Allocation: The funds tied up in buffer inventory could be used for other investments or business expansion opportunities.
- Risk of Obsolescence: Excess buffer inventory may become obsolete if customer demand changes, technology evolves, or products are updated.
- Complexity in Management: Maintaining and managing buffer inventory requires accurate forecasting, demand planning, and inventory control to strike the right balance.
- Reduced Inventory Turnover: Excessive buffer inventory can lead to slower inventory turnover, which impacts the overall efficiency of working capital utilization.
- Potentially Higher Order Quantities: It might lead to larger order quantities than necessary, resulting in additional holding costs and increased lead times.
- Impact on Lean Practices: For businesses aiming to implement lean practices and reduce waste, excessive buffer inventory can contradict these goals by adding unnecessary inventory in the system.
- Inaccurate Forecasting Challenges: Relying solely on buffer inventory without improving demand forecasting accuracy can lead to unnecessary holding costs or stockouts if the buffer is insufficient.
In summary, while buffer inventory provides essential risk mitigation and operational benefits, it also comes with potential costs and complexities. The key to effective buffer inventory management is finding the right balance between meeting customer demands and minimizing the associated costs. Businesses should carefully assess their specific circumstances, industry dynamics, and supply chain characteristics when determining the optimal level of buffer inventory to maintain.
Why you need to keep buffer inventory

Buffer inventory, also known as safety stock, is maintained for several important reasons:
Demand Variability
Customer demand can be unpredictable, subject to seasonal fluctuations, market trends, and other external factors. It ensures that a business can meet unexpected spikes in demand without experiencing stockouts. This helps maintain customer satisfaction and prevents missed sales opportunities.
Supply Variability
Suppliers may face disruptions, delays, or quality issues that affect the timely delivery of materials or products. It acts as a cushion against such supply chain uncertainties, preventing production stoppages or delays caused by shortages.
Lead Time Variability
The time it takes for suppliers to deliver materials or products can vary due to factors like transportation delays, production bottlenecks, or unforeseen events. It compensates for these variations, ensuring that production can continue even if suppliers face delays.
Uncertainty and Risk Management
In an ever-changing business environment, uncertainties are inevitable. It serves as a risk mitigation strategy by providing a safety net against unexpected disruptions, helping businesses navigate through unforeseen challenges without severe negative impacts.
Supplier Relationships
Having buffer inventory can foster positive relationships with suppliers. When a business can maintain consistent orders despite minor fluctuations in demand, suppliers may be more willing to work closely and prioritize their needs.
Avoiding Stockouts
Stockouts can lead to customer dissatisfaction, lost sales, and potential damage to a company’s reputation. It prevents stockouts by ensuring that products are available for customers even when demand is higher than expected.
Maintaining Service Levels
It helps companies maintain a desired level of service to customers. It allows businesses to commit to certain delivery times and service guarantees without the risk of being unable to fulfill their promises.
Production Efficiency
Buffer inventory can help smoothen production processes by providing a buffer against minor disruptions. This can lead to more stable production schedules and reduced production bottlenecks.
Mitigating Lead Time Fluctuations
When lead times vary due to factors like supplier capacity constraints or transportation issues, It compensates for these fluctuations, helping companies meet their commitments to customers.
Economic Order Quantity (EOQ) Considerations
In certain cases, ordering larger quantities to include buffer inventory can result in cost savings due to economies of scale in production or reduced ordering frequency.
In essence, it is a strategic tool that provides a safety cushion against the uncertainties inherent in supply chain management. It allows businesses to maintain stability, manage risks, and uphold customer satisfaction, even in the face of unexpected events and fluctuations.