In the intricate world of supply chain management and inventory control, the concept of “fill rate” serves as a vital barometer of efficiency and customer satisfaction. But did you know that there isn’t just one universal fill rate? Instead, the fill rate metric takes on various forms, each offering a unique perspective on different aspects of order fulfillment and inventory performance.
In this post, we embark on a journey to unravel the multifaceted nature of it, delving into the diverse types that allow businesses to fine-tune their operations and cater to specific objectives.
What is a good fill rate?
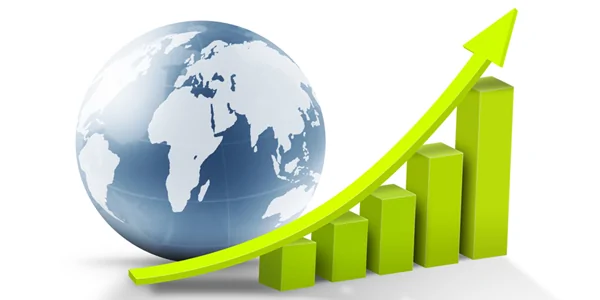
A “good” fill rate can vary depending on the industry, the specific business, and customer expectations. What constitutes a good fill rate for one company may not be the same for another. Generally, it is one that meets or exceeds customer expectations while maintaining cost-effective inventory management. Here are some considerations:
Customer Expectations
The most critical factor in determining a good fill rate is meeting or exceeding customer expectations. Different industries and customer segments may have varying expectations. For some, a 95% may be considered excellent, while in other industries, such as healthcare or critical manufacturing, a fill rate approaching 100% might be expected.
Industry Standards
Some industries have established benchmarks for what constitutes a good fill rate. For example, the retail industry often aims for a fill rate of 95% or higher, as customers typically expect products to be in stock and readily available. However, industries like aerospace or defense might demand fill rates closer to 100% due to critical supply chain requirements.
Product Characteristics
The type of products being sold can also influence what is considered a good fill rate. Perishable goods or products with seasonal demand may require higher fill rates to avoid waste and meet customer needs during peak periods.
Service Level Agreements (SLAs)
In business-to-business (B2B) transactions, contracts or SLAs with customers may specify required fill rate levels. Meeting these contractual obligations is essential to maintain healthy customer relationships.
Supply Chain Complexity
The complexity of a supply chain can impact fill rate expectations. Businesses with global supply chains may face more significant challenges in achieving high fill rates due to transportation and logistics complexities.
Costs
Balancing a high fill rate with inventory carrying costs is crucial. Achieving a 100% fill rate might require excessive safety stock, leading to higher storage and holding costs. A good fill rate should strike a balance between meeting customer needs and cost-effectiveness.
Historical Performance
It can also be relative to a company’s historical performance. If a business has consistently improved its fill rate over time, its current rate may be considered good in the context of its own progress.
In summary, there is no one-size-fits-all answer to what constitutes a good fill rate. It depends on various factors, including industry norms, customer expectations, product characteristics, and cost considerations. The key is to align goals with customer needs and business objectives while optimizing supply chain efficiency and cost-effectiveness. Businesses should regularly assess their fill rate performance and make adjustments as necessary to remain competitive and meet customer demands.
Types of fill rate
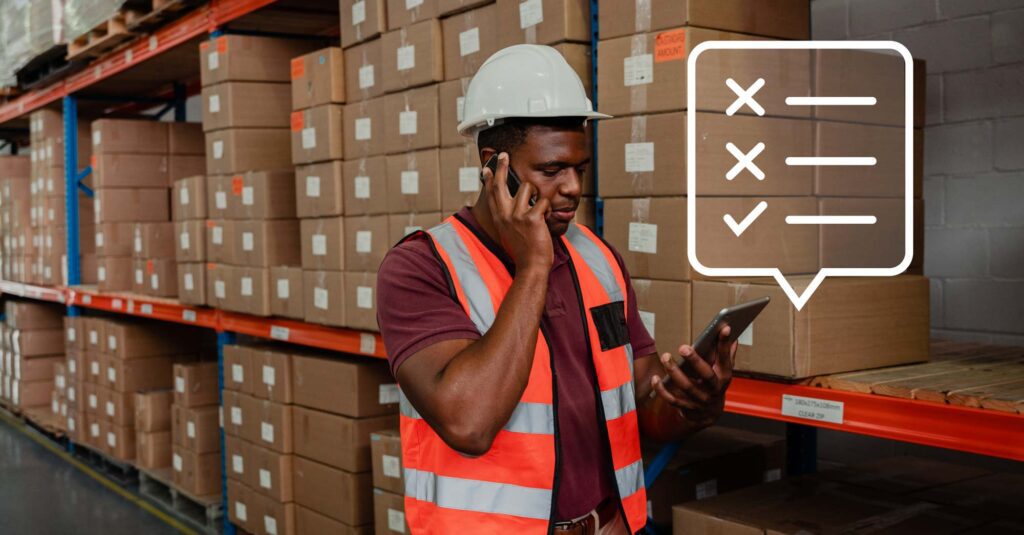
There are several types that businesses and organizations may use to measure and evaluate different aspects of their operations. Here are some common types:
Line
It assesses the percentage of customer orders or product lines that are fulfilled in their entirety without any stockouts or backorders. It measures how often an entire order or product line is delivered without any missing items.
Item
It calculates the percentage of individual items within customer orders that are successfully fulfilled without stockouts. It focuses on the completeness of each item within an order. Regardless of whether the entire order is fulfilled.
Order
It measures the percentage of customer orders that are completely fulfilled without any stockouts or backorders. It assesses the overall order fulfillment performance and customer satisfaction.
Case
It evaluates the percentage of cases or cartons of products that are delivered in full without any missing items. It is often used in industries where products are shipped in bulk cases.
Line Item
It looks at the completeness of individual line items within customer orders. It calculates the percentage of line items that are fulfilled without stockouts, even if other items in the same order are backordered.
Service Level
It is commonly used in supply chain management and logistics. Representing the percentage of customer demand or orders that are fulfilled within a specific lead time or service level agreement (SLA). It takes into account not only what is fulfilled but also how quickly it is delivered.
Backorder
It specifically measures the percentage of backordered items that are successfully fulfilled and delivered to customers once the items become available in inventory. It assesses how effectively a company manages backorders.
Perfect Order
It evaluates how well a company meets all aspects of an ideal or “perfect” order. It includes criteria such as on-time delivery, complete order fulfillment, and accurate invoicing. This metric aims to measure overall order quality.
Supplier
It assesses the performance of suppliers in delivering products or materials on time and in the quantities requested by the purchasing company. It measures how well suppliers meet their obligations.
Demand
It is a measure of how well a company satisfies customer demand or sales orders based on their forecasts and demand predictions. It helps evaluate the accuracy of demand forecasting.
The choice of which fill rate type to use depends on the specific goals and needs of a business or organization. Different industries and contexts may prioritize different fill rate metrics to assess and improve their supply chain and customer service performance.
Why calculate fill rate?
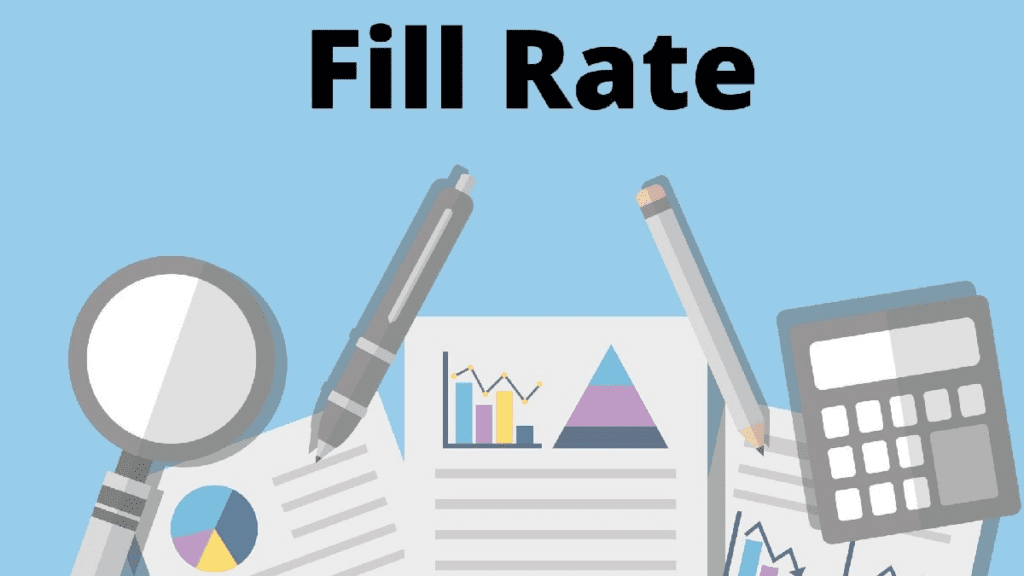
Calculating it is essential for several reasons, as it provides valuable insights and benefits for businesses involved in inventory management and supply chain operations:
Customer Satisfaction
One of the primary reasons to calculate it is to ensure customer satisfaction. When a company consistently fulfills customer orders without stockouts or backorders, it leads to happy customers who receive their products on time. Satisfied customers are more likely to return for future purchases and recommend the business to others.
Inventory Management
It helps in optimizing inventory levels. By measuring how well you are meeting customer demand, you can adjust your inventory management strategies. A high fill rate suggests efficient inventory control, while a low fill rate might indicate the need to increase stock levels or improve supply chain processes.
Lost Sales Reduction
A low fill rate often results in lost sales, where customers go elsewhere to find the products they need. By improving it, businesses can reduce the revenue lost due to missed sales opportunities.
Cost Efficiency
Maintaining excessive inventory can be costly due to storage, carrying, and handling expenses. Conversely, a low fill rate may force businesses into expedited shipping or production, incurring additional costs. Calculating it helps strike a balance between meeting customer demand and avoiding unnecessary carrying costs.
Supply Chain Performance Evaluation
It is a key performance indicator for supply chain management. It allows businesses to assess the effectiveness of their supply chain processes, including order processing, production, warehousing, and distribution.
Demand Forecasting
Accurate fill rate data can improve demand forecasting. When you have a better understanding of how often you meet customer demand, you can make more precise predictions about future demand patterns and adjust your procurement and production strategies accordingly.
Customer Retention
High fill rates contribute to customer loyalty and retention. Customers are more likely to stick with a company that consistently delivers products on time and in full. Loyal customers often become repeat buyers, generating long-term revenue for the business.
Competitive Advantage
In many industries, a high fill rate can set a business apart from competitors. It can be a selling point that attracts customers who prioritize reliable and prompt order fulfillment.
In summary, calculating it is crucial for businesses to enhance customer satisfaction, optimize inventory management, reduce costs, evaluate supply chain performance, and maintain a competitive edge. It is a valuable metric that informs decision-making and helps businesses fine-tune their operations for improved efficiency and profitability.
What is the difference between fill rate and inventory turnover?
There are both important metrics in inventory management, but they measure different aspects of a company’s inventory performance. Here’s some key differences:
Definition:
Fill Rate: It measures how effectively a company fulfills customer orders or demand for its products. It assesses the percentage of customer orders that are successfully and completely filled without stockouts or backorders.
Inventory Turnover: Inventory turnover, also known as inventory turnover ratio, calculates how efficiently a company manages its inventory.
Focus:
Fill Rate: It focuses on customer satisfaction and order fulfillment. It indicates whether the company is meeting customer demand and delivering products promptly.
Inventory Turnover: Inventory turnover focuses on inventory efficiency and the capital tied up in inventory. It shows how effectively a company is utilizing its inventory to generate sales.
Calculation:
Fill Rate: It is calculated as a percentage and is determined by dividing the total quantity of customer orders fulfilled without stockouts by the total customer demand during a specific period.
Inventory Turnover: Inventory turnover is typically calculated as a ratio and is determined by dividing the cost of goods sold (COGS) by the average inventory value during a specific period. The formula is as follows:
Inventory Turnover Ratio = COGS / Average Inventory
Purpose:
Fill Rate: The primary purpose is to assess customer service levels and ensure customer satisfaction. It helps identify and rectify issues related to stockouts, backorders, and order fulfillment.
Inventory Turnover: The primary purpose of inventory turnover is to evaluate inventory management efficiency and the speed at which inventory is converted into sales. It helps determine optimal inventory levels and identifies slow-moving or obsolete items.
Time Frame:
Fill Rate: It is typically measured for a specific time frame, such as daily, weekly, or monthly, to assess the recent performance in fulfilling customer orders.
Inventory Turnover: Inventory turnover is usually calculated annually or over a longer time frame to provide a broad perspective on how efficiently inventory is managed throughout the year.
Outcome:
Fill Rate: A high fill rate indicates that the company is doing well in meeting customer demand and ensuring customer satisfaction. Conversely, a low fill rate suggests that there are issues with order fulfillment.
Inventory Turnover: A high inventory turnover ratio implies that a company is efficiently managing its inventory and minimizing excess stock.
In summary, fill rate and inventory turnover serve different purposes and provide insights into distinct aspects of inventory management. It focuses on customer service and order fulfillment, while inventory turnover assesses inventory efficiency and capital utilization. Both metrics are valuable for businesses in optimizing their supply chain and inventory operations.