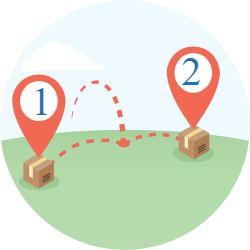
Managing shipments efficiently is a critical aspect of supply chain and logistics operations. One common challenge faced in this process is the occurrence of split shipments. But what exactly is a split shipment, and how can businesses navigate this issue to improve their operations and customer satisfaction? In this article, we will explore the concept of split shipments and delve into strategies on how to avoid them.
What is a split shipment?
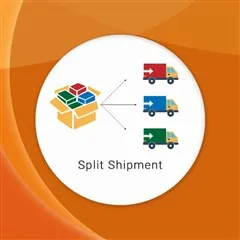
A split shipment refers to a situation in which an order or shipment of goods is divided into multiple shipments that are sent at different times or to different locations. This can happen for various reasons, and it’s common in the logistics and supply chain management industry.
Why are split shipments used?

Split shipments are used for several reasons in the logistics and supply chain management industry. Here are three primary reasons for using split shipments:
Partial Availability
Sometimes, not all the items in an order are available for immediate shipment. Split shipments are used to send the available items to the customer promptly, rather than delaying the entire order. This helps in providing a better customer experience and ensures that customers receive at least some of the items in a timely manner.
Inventory Management
Split shipments can help companies manage their inventory more effectively. By shipping items from different locations or suppliers, businesses can balance their stock levels and optimize the use of available resources. This can lead to better control of inventory costs and reduce the risk of overstocking or understocking.
Shipping Constraints
There are various shipping constraints and limitations, such as weight limits, volume restrictions, or destination-specific regulations. Split shipments can be used to comply with these constraints. For example, when shipping internationally, some items may need to be sent separately due to specific customs or regulatory requirements. Split shipments can also be used to avoid exceeding weight or size limits for certain shipping methods.
Overall, split shipments are a practical solution for ensuring timely delivery, effective inventory management, and compliance with various logistical constraints. While they can add complexity to the shipping process, they are often essential for meeting customer expectations and maintaining efficient supply chain operations.
What is the problem with split shipment?
Split shipments can pose several challenges and problems for businesses and customers. Some of the common issues associated with split shipments include:
- Increased Shipping Costs: Split shipments often result in multiple shipments, which can significantly increase shipping costs for both the business and the customer. This can impact the overall profitability of an order.
- Shipping Complexity: Managing multiple shipments can be administratively complex. It requires additional coordination, documentation, and tracking, which can lead to errors and delays.
- Customer Dissatisfaction: Customers may be frustrated when they receive only part of their order and have to wait for the remaining items. This can lead to a negative customer experience and potentially harm the reputation of the business.
- Operational Inefficiencies: Split shipments can disrupt warehouse and fulfillment operations. It may lead to suboptimal use of space, resources, and labor.
- Inventory Management Challenges: Maintaining proper inventory levels and ensuring availability of items for immediate shipment can be more challenging when split shipments are frequent.
While split shipments may be unavoidable in some cases, businesses need to find a balance between the need for efficient inventory management and the goal of providing a positive customer experience. Effective communication and strategies to minimize the problems associated with split shipments are essential for mitigating their impact on operations and customer satisfaction.
How to avoid split shipments
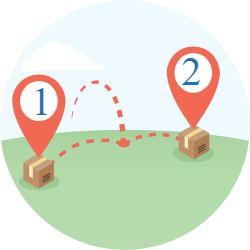
Avoiding split shipments can be challenging in certain situations, especially when dealing with complex supply chains or logistics constraints. However, there are strategies you can implement to reduce the frequency of split shipments:
Inventory Management:
- Maintain adequate stock levels of popular items to minimize the occurrence of partial availability.
- Implement demand forecasting and reorder points to optimize inventory levels.
- Centralize inventory if possible, reducing the need to source items from multiple locations.
Supplier and Vendor Relationships:
- Build strong relationships with suppliers and vendors to ensure a steady and reliable supply of goods.
- Collaborate with suppliers to improve lead times and minimize out-of-stock situations.
Shipping and Logistics Planning:
- Use efficient order fulfillment and shipping processes to minimize the need for split shipments.
- Optimize your order picking and packing processes to reduce errors and backorders.
- Choose shipping methods and carriers that can handle larger volumes and weights, reducing the likelihood of weight or size constraints.
Inventory Visibility:
- Implement inventory tracking and management systems to have real-time visibility into stock levels.
- Use integrated software solutions that allow you to see the availability of all items in real-time, helping you make informed shipping decisions.
Customer Communication:
- Clearly communicate with customers about the availability and expected shipping times of their orders.
- Offer customers the option to group items or wait for all items to be available before shipping, if it aligns with their preferences.
Keep in mind that completely eliminating split shipments may not be possible in all situations, and it might not always be the most cost-effective or efficient solution. It’s essential to strike a balance between avoiding split shipments and ensuring efficient inventory management, cost-effectiveness, and customer satisfaction. Continuously assess your processes and adapt your strategies based on changing business needs and customer preferences.