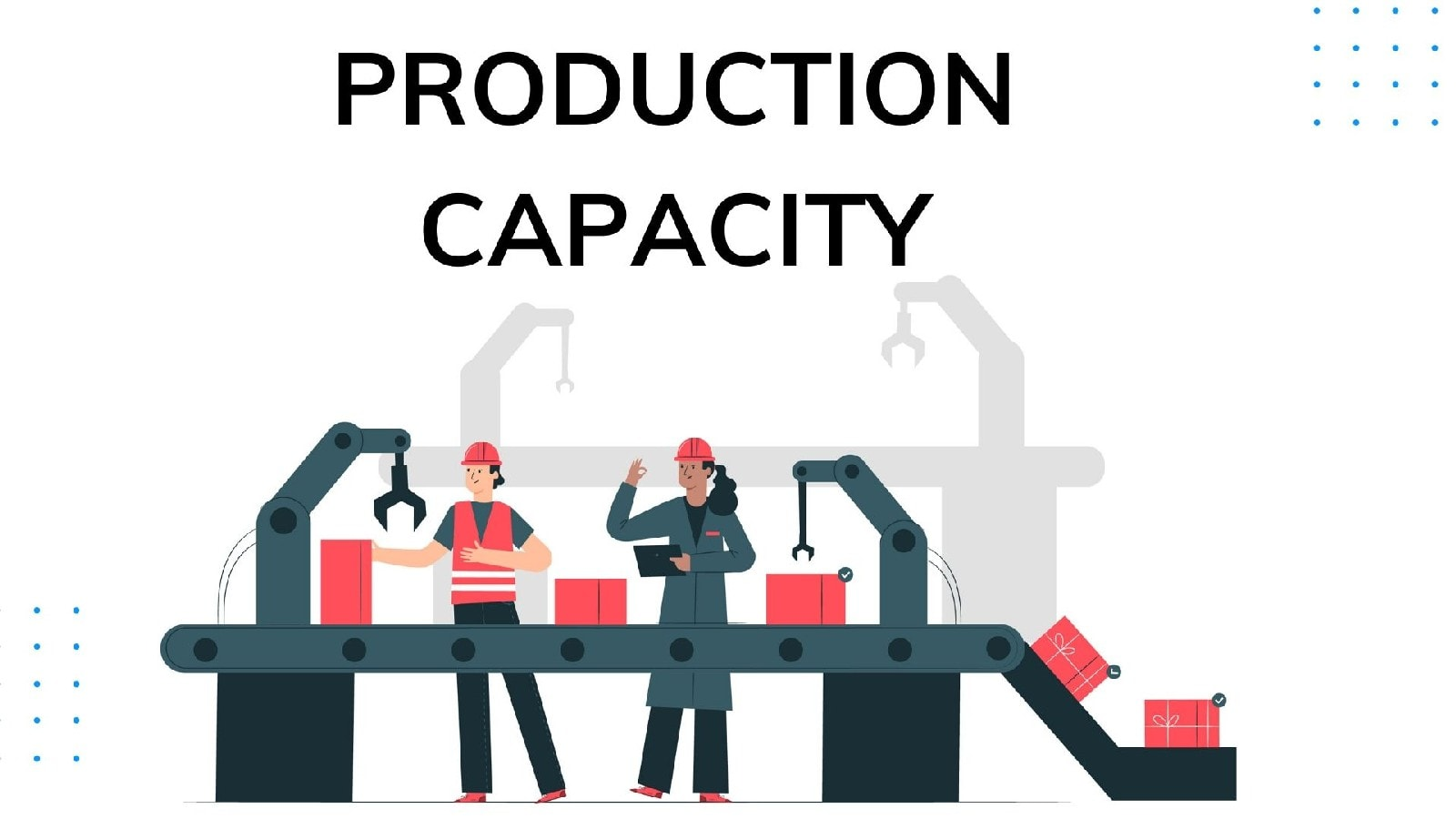
Production capacity is a pivotal metric that defines the ability of a business to meet the demands of its market while maximizing resource utilization. Understanding what production capacity entails and how to calculate it is crucial for businesses striving to optimize efficiency and maintain competitiveness in today’s dynamic markets.
In this exploration, we delve into the concept of production capacity, examining its significance in the manufacturing landscape.
What is Production Capacity?
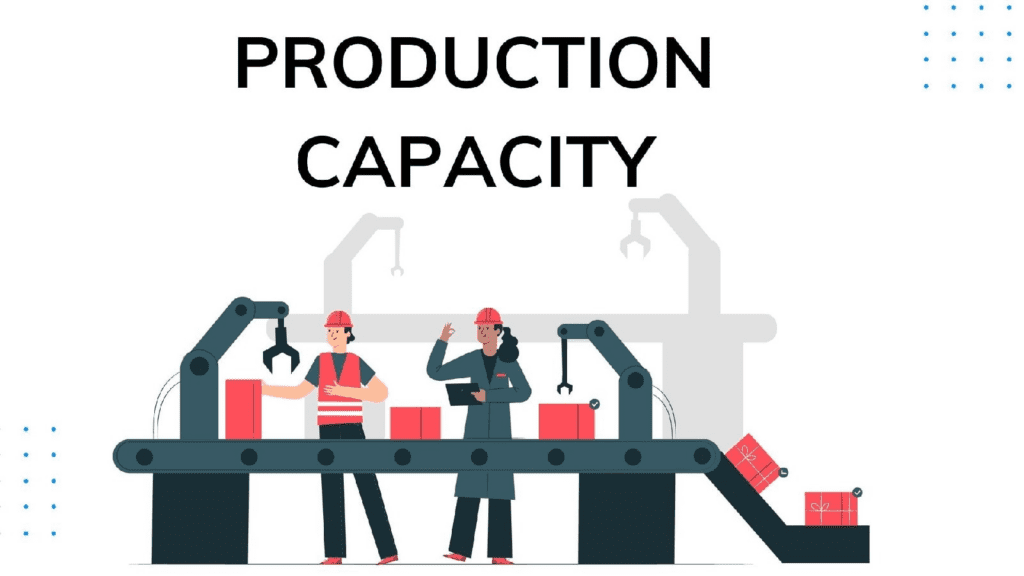
Production capacity refers to the maximum output or volume of goods and services that a company can produce using its available resources, such as equipment, labor, technology, and time, during a specific period. It is a key measure for businesses to understand their capabilities and to plan their operations effectively.
What does high production capacity mean?
High production capacity refers to a situation in which a business or a production system can generate a significant volume of goods or services within a given timeframe. Essentially, it implies that the organization possesses the capability to produce a large quantity of output, often surpassing current market demand. A high production capacity is indicative of the ability to scale operations and meet increased or fluctuating demand without straining resources.
How to calculate production capacity?

Calculating production capacity involves assessing the maximum output a production system can achieve based on its available resources and constraints. The specific method of calculation can vary depending on the nature of the production process and the industry. Here’s a general guide on how to calculate production capacity:
Identify Key Parameters:
Time Period:
- Determine the time period for which you want to calculate production capacity (e.g., per day, per week, per month).
Production Units:
- Define the unit of production (e.g., number of units, tons, dollars).
Gather Data:
Maximum Available Time:
- Identify the total available production time during the chosen period. This is the time when production can take place, excluding breaks, maintenance, and downtime.
Production Rate per Unit of Time:
- Determine the rate at which products or services are produced per unit of time. This could be based on historical data, equipment specifications, or operational parameters.
Use the Formula:
The basic formula for calculating production capacity is:
Production Capacity=Maximum Available Time×Production Rate per Unit of TimeProduction Capacity=Maximum Available Time×Production Rate per Unit of Time
Example:
Let’s say you operate a manufacturing facility for widgets. Your facility runs 24 hours a day (1,440 minutes) and produces 60 widgets per hour.
Production Capacity=1,440 minutes/day×60 widgets/hourProduction Capacity=1,440minutes/day×60widgets/hour
Production Capacity=86,400 widgets/dayProduction Capacity=86,400widgets/day
Consider Efficiency and Constraints:
In reality, the production process may not run at maximum efficiency all the time. Therefore, it’s important to consider factors such as machine downtime, maintenance, and other constraints that may affect actual production capacity.
Continuous Monitoring and Adjustment:
Production capacity is not a fixed value; it can change over time due to factors like equipment upgrades, process improvements, or changes in workforce efficiency. Regularly monitor and update your production capacity calculations to reflect any changes in the production system.
Keep in mind that this is a simplified approach, and the actual calculation may involve more complex considerations based on the specific characteristics of your production process.
How to increase production capacity?
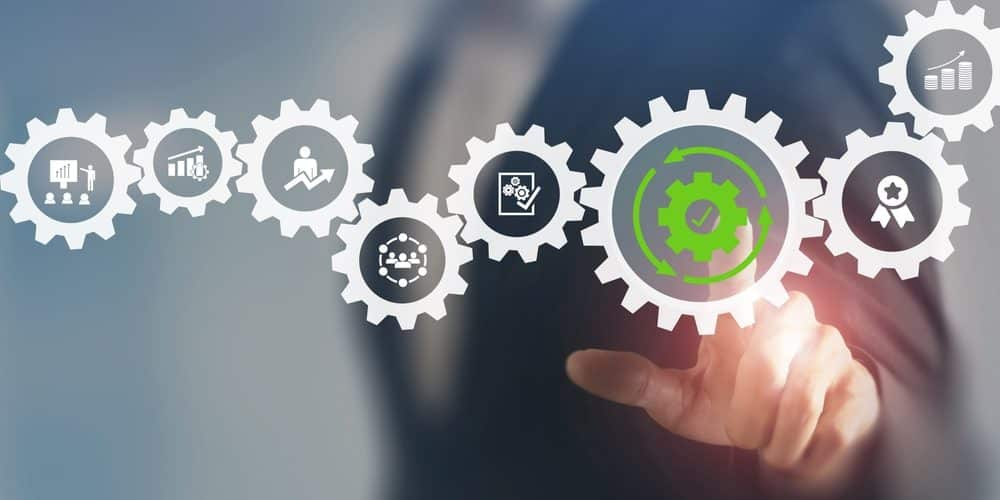
Increasing production capacity is a strategic goal for many businesses aiming to meet growing demand or improve operational efficiency. Here are five general strategies to increase :
Improve Operational Efficiency:
- Optimize Processes: Identify and eliminate bottlenecks or inefficiencies in your production processes. Streamlining workflows and minimizing downtime can enhance overall efficiency.
- Implement Lean Manufacturing: Apply lean principles to reduce waste, improve resource utilization, and enhance the flow of production.
Invest in Technology and Automation:
- Upgrade Equipment: Invest in modern and efficient machinery that can increase production speed and accuracy. Upgrading technology can lead to higher throughput.
- Automation: Introduce automation to handle repetitive tasks, reducing the reliance on manual labor and increasing production efficiency.
Workforce Training and Development:
- Skill Enhancement: Train your workforce to improve their skills and efficiency. Well-trained employees can contribute to faster and more accurate production.
- Cross-Training: Cross-train employees to handle multiple roles within the production process, enabling flexibility and smoother operations.
Expand Facilities or Production Lines:
- Facility Expansion: If feasible, consider expanding your production facilities to accommodate higher production volumes. This may involve increasing the size of your existing facility or opening new ones.
- Add Production Lines: Introduce additional production lines to parallelize the manufacturing process and increase overall output.
Optimize Supply Chain and Inventory Management:
- Supplier Relationships: Strengthen relationships with suppliers to ensure a steady and timely supply of raw materials. This reduces the risk of production delays due to shortages.
- Inventory Optimization: Implement just-in-time (JIT) inventory systems to minimize excess inventory and associated carrying costs while ensuring that materials are available when needed.
Remember that the effectiveness of these strategies may vary depending on the specific industry, market conditions, and the nature of your production processes. It’s advisable to conduct a thorough analysis and, if necessary, seek the guidance of industry experts or consultants to tailor these strategies to your unique situation.