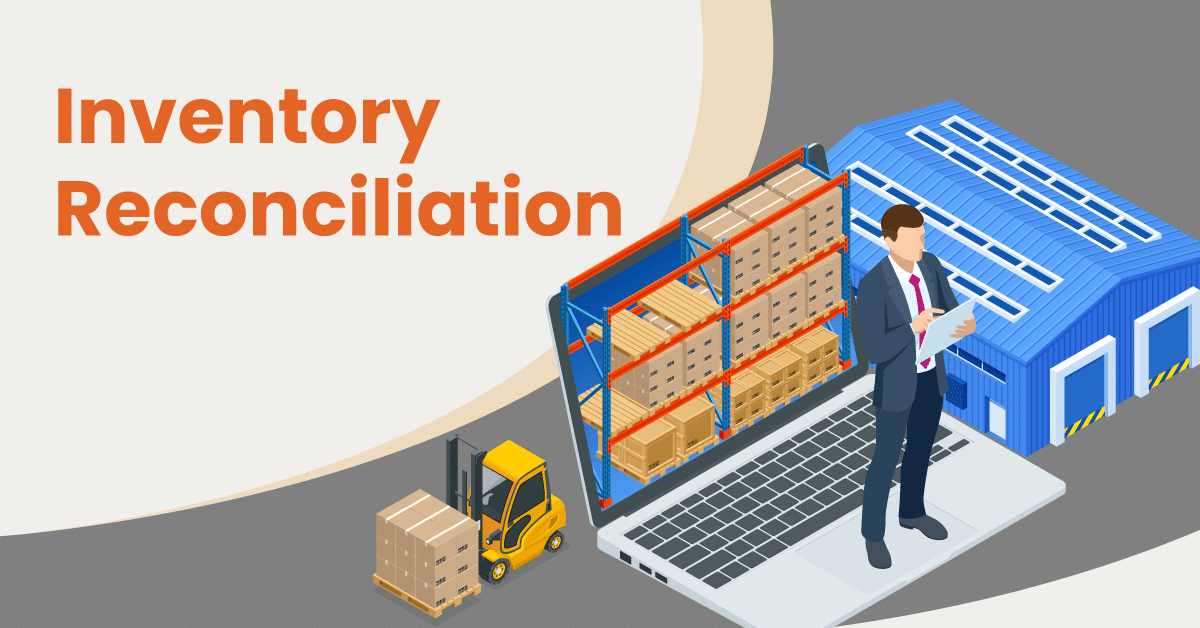
Effectively managing inventory is a cornerstone of successful supply chain management, and maintaining accurate records is paramount to this process. The post explores the diverse approaches businesses employ to align physical stock levels with recorded inventory data. In the dynamic landscape of modern commerce, where precision and agility are vital, businesses seek robust methods to ensure the integrity of their inventory information.
This exploration delves into three distinct methodologies for inventory reconciliation, each presenting its own set of advantages and challenges.
What is inventory reconciliation
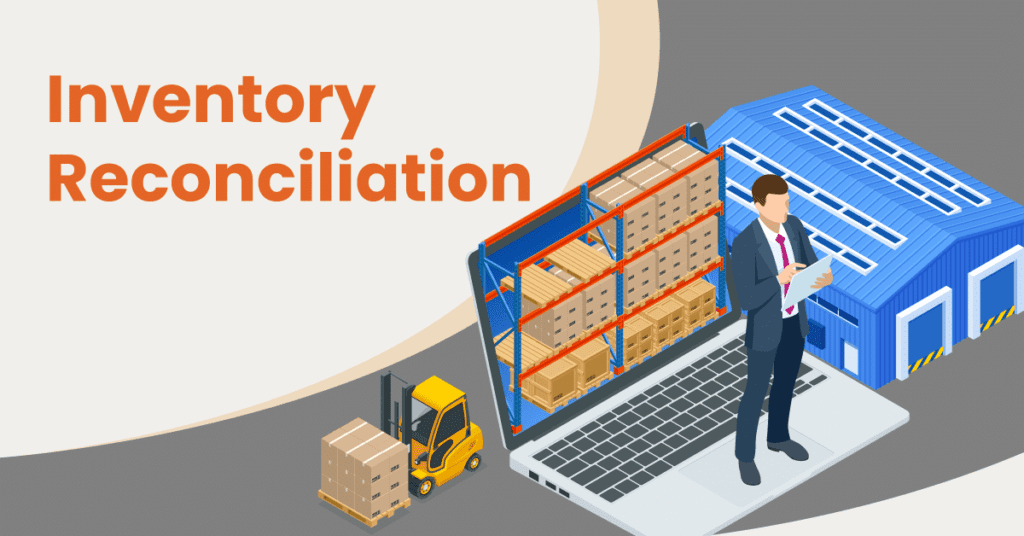
Inventory reconciliation is the process of comparing and aligning the physical inventory on hand with the recorded inventory levels in a company’s books or inventory management system. The goal is to identify and rectify any discrepancies between the actual quantity of goods in stock and the quantity recorded in the accounting or inventory records. This process is crucial for maintaining accurate financial records, optimizing supply chain efficiency, and preventing issues such as stockouts or overstocking.
3 methods for performing an inventory reconciliation
Performing inventory reconciliation involves comparing the physical count of goods with the recorded inventory levels in the system. Here are three common methods for conducting inventory reconciliation:
Periodic Physical Counts:
- Process: Conduct physical counts of all items in stock at regular intervals, such as monthly, quarterly, or annually. This involves physically counting each item and comparing the results with the recorded quantities in the inventory management system.
- Advantages:
- Provides a comprehensive and detailed overview of the entire inventory.
- Suitable for businesses with a relatively stable and predictable demand for products.
- Challenges:
- Disruptive to daily operations as it often requires a temporary halt in warehouse activities.
- May not catch discrepancies that occur between the counting periods.
Cycle Counting:
- Process: Divide the inventory into smaller, manageable subsets, and regularly count a portion of the inventory on a rotating basis. The subsets can be based on ABC analysis (categorizing items by value), product categories, or storage locations.
- Advantages:
- Minimizes disruption to daily operations as only a subset of inventory is counted at a time.
- Enables more frequent checks, helping to identify and address discrepancies sooner.
- Challenges:
- Requires careful planning to ensure that all items are counted within a defined cycle.
- May not provide a complete picture of the entire inventory at once.
Technology-Assisted Reconciliation:
- Process: Implement technology solutions such as barcode scanners, RFID systems, or automated inventory management software to streamline the reconciliation process. These technologies can improve accuracy, reduce human error, and provide real-time data.
- Advantages:
- Enhances efficiency by speeding up the counting process and minimizing errors associated with manual data entry.
- Provides real-time visibility into inventory levels, enabling prompt identification and resolution of discrepancies.
- Challenges:
- Initial investment in technology and training may be required.
- Regular maintenance and updates are necessary to ensure the ongoing accuracy of technology-assisted systems.
Each method has its advantages and challenges, and the choice of the most suitable method depends on factors such as the size of the inventory, the nature of the products, and the resources available to the business. Some companies may use a combination of these methods to create a comprehensive and effective inventory reconciliation process.
The benefits of inventory reconciliation
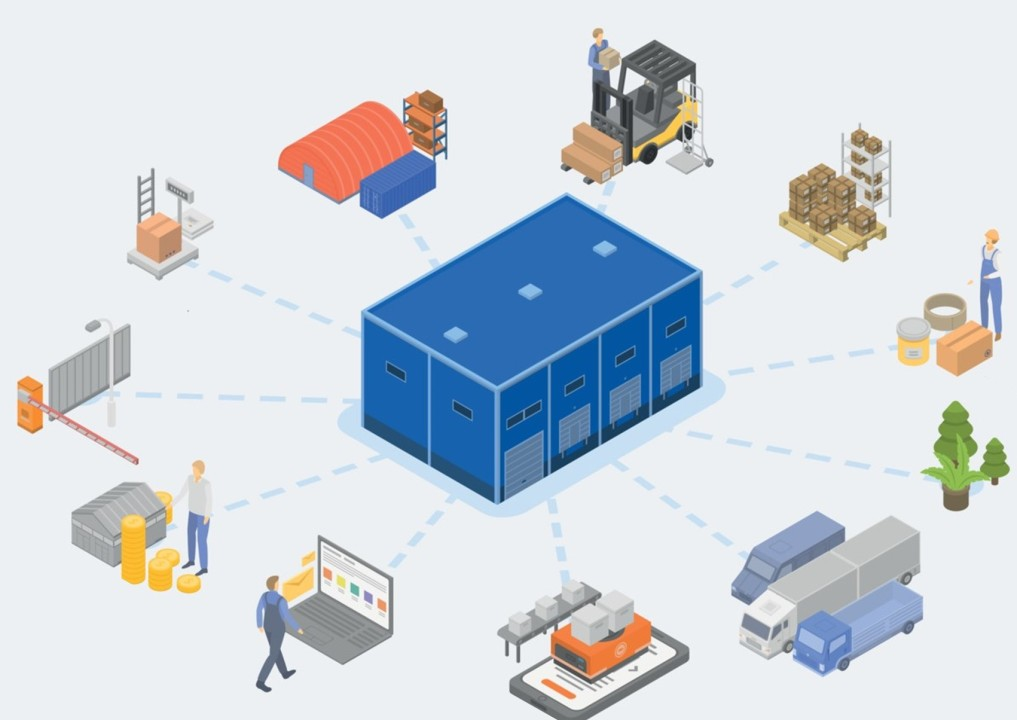
Inventory reconciliation offers several benefits to businesses, helping them maintain accurate records, improve operational efficiency, and make informed decisions. Here are five key benefits:
Accurate Financial Reporting:
- Precision in Financial Statements: Inventory reconciliation ensures that the values reported in financial statements accurately reflect the actual value of goods on hand. This accuracy is crucial for financial reporting, budgeting, and forecasting, providing stakeholders with a clear and reliable picture of the company’s financial health.
Prevention of Stockouts and Overstocking:
- Optimized Inventory Levels: By reconciling inventory regularly, businesses can identify and address discrepancies promptly. This helps in maintaining optimal stock levels, preventing stockouts that can lead to lost sales or customer dissatisfaction, as well as avoiding overstock situations that tie up capital and warehouse space.
Improved Operational Efficiency:
- Streamlined Processes: Accurate inventory records, resulting from reconciliation efforts, contribute to streamlined and efficient warehouse operations. It reduces the time and effort spent searching for misplaced items, enables better order fulfillment, and enhances overall supply chain efficiency.
Cost Savings:
- Reduction in Holding Costs: Effective inventory reconciliation helps in minimizing excess inventory, reducing holding costs associated with storage, insurance, and depreciation. By aligning inventory levels with actual demand, businesses can optimize cash flow and allocate resources more efficiently.
Enhanced Decision-Making:
- Informed Strategic Planning: Accurate and up-to-date inventory data allows for more informed decision-making. Businesses can analyze trends, identify slow-moving or obsolete items, and make strategic decisions on procurement, production, and sales. This leads to a more agile and responsive supply chain.
In summary, inventory reconciliation is a fundamental practice that goes beyond mere record-keeping. It contributes to the overall health and efficiency of a business by ensuring financial accuracy, preventing stock-related issues, optimizing operations, reducing costs, and empowering strategic decision-making. Regular and thorough inventory reconciliation is an essential aspect of effective supply chain management.
How to Reconcile Your Inventory in 5 Steps
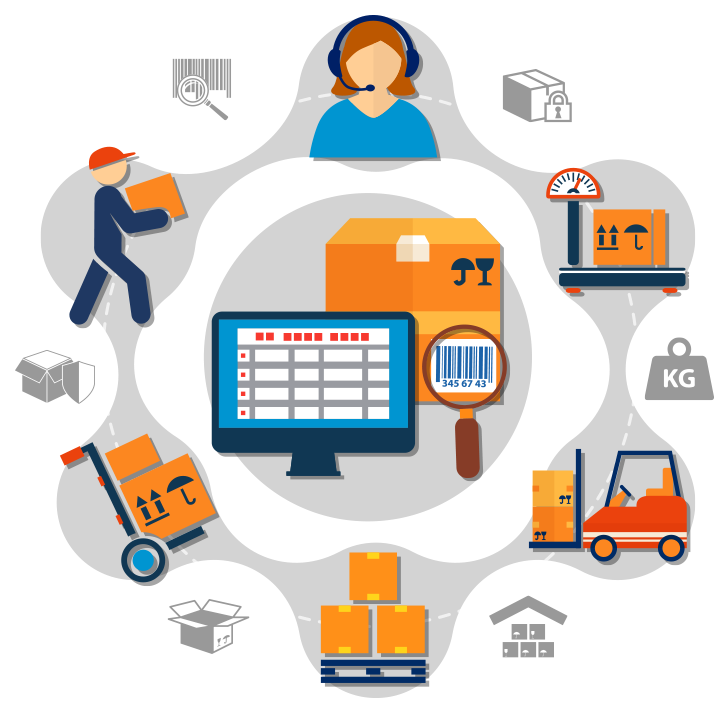
Reconciling inventory is a crucial process to ensure accuracy in tracking stock levels and maintaining an efficient supply chain. Here are five steps to effectively reconcile your inventory:
Establish a Baseline:
- Begin by creating a comprehensive and accurate baseline of your current inventory. This includes recording the quantity of each product, its location within the warehouse, and any relevant details such as batch or serial numbers.
Regular Physical Counts:
- Conduct regular physical counts of your inventory to compare against the recorded levels in your system. Schedule these counts based on the turnover rate of your products. This process helps identify discrepancies between the physical count and the recorded data.
Utilize Technology:
- Leverage inventory management software and technologies, such as barcode scanners or RFID systems, to streamline the reconciliation process. These tools can significantly reduce errors and enhance the efficiency of data collection during physical counts.
Investigate Discrepancies:
- When discrepancies are identified between physical counts and recorded inventory levels, promptly investigate the root causes. Common reasons for discrepancies may include data entry errors, theft, damaged goods, or inaccuracies in the initial baseline recording.
Implement Cycle Counting:
- Instead of relying solely on periodic full physical counts, consider implementing a cycle counting system. This involves regularly counting a subset of your inventory, rotating through different products or sections of the warehouse. This ongoing approach helps catch discrepancies more frequently and allows for quicker corrective actions.
By following these five steps, businesses can establish a robust process for reconciling their inventory, promoting accuracy, and minimizing the risk of stockouts or overstocks. Regularly reconciling inventory not only ensures that your records align with the actual stock levels but also enhances the overall efficiency and reliability of your supply chain management.